靶材利用率提升技术:降低生产成本、提高材料利用效率的有效途径
1. 磁控溅射靶材利用率:冰山之下的成本与资源隐忧
磁控溅射的精髓在于利用等离子体,如同微观世界的“刻刀”,将靶材表面的原子剥离,使其沉积在基片上,最终形成功能各异的薄膜。然而,理想与现实之间存在着巨大的鸿沟。 我们期望靶材能够被“物尽其用”,均匀损耗,每一颗溅射原子都能精准地落在基片之上。然而,实际的溅射过程却远比想象中复杂,多种物理现象交织,导致了靶材利用率的普遍低下。
1.1 非均匀腐蚀: “跑道效应”与材料的隐性浪费
传统磁控溅射,如同在靶材表面“画”出了一条条深深的跑道。 这种“跑道型腐蚀”并非偶然,而是磁场、等离子体与靶材相互作用的必然结果。磁场强度在靶材表面并非均匀分布,通常在磁极中心区域形成磁场强度较高的区域,而在其他区域磁场强度相对较弱。等离子体在磁场的作用下,更容易聚集在磁场强度较高的区域,导致该区域的等离子体密度远高于其他区域。 这种等离子体密度的不均匀性,直接导致了靶材表面溅射速率的差异。 等离子体密度高的区域,靶材原子被更强烈地溅射出来,腐蚀速度更快,最终形成了肉眼可见的“跑道”;而等离子体密度低的区域,靶材腐蚀则相对缓慢,甚至几乎没有腐蚀。
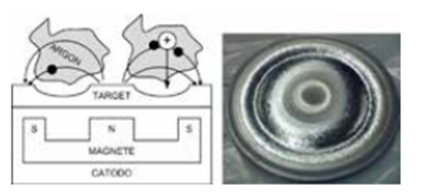
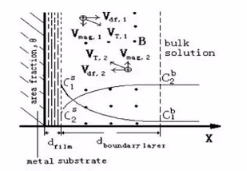
这种非均匀腐蚀的直接后果,就是靶材中心区域的材料可能仍完好如初,但“跑道”区域的材料却已消耗殆尽,不得不更换靶材。 这意味着,大量的靶材材料在尚未充分利用的情况下就被迫废弃,造成了巨大的浪费。 更令人担忧的是,这种浪费往往是隐性的,不易察觉,长期累积下来,会显著增加生产成本。
1.2 边缘效应: 被忽视的角落,被浪费的材料
靶材的边缘区域,如同被遗忘的角落,常常被忽视,但这里的材料利用率同样不容乐观。 在磁控溅射系统中,用于约束等离子体的磁场通常集中在靶材的中心区域,边缘区域的磁场强度相对较弱,导致等离子体密度也随之降低。 较低的等离子体密度意味着较低的溅射效率,靶材边缘区域的材料往往难以被有效溅射出来。 此外,边缘区域的溅射原子,由于缺乏有效的约束,更容易发生散射,沉积到腔体壁上,而非目标基片上,进一步降低了材料的利用效率。
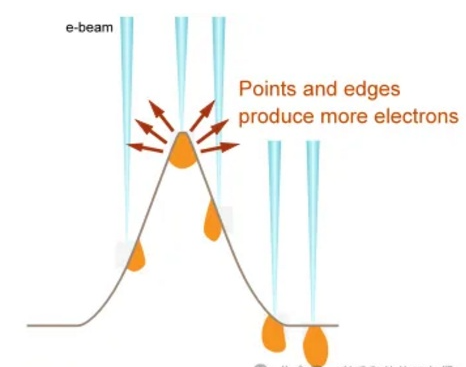
据统计,在某些传统的磁控溅射工艺中,靶材边缘区域的材料浪费可能高达 10%-20%,这无疑是一笔巨大的损失。 尤其是在使用大尺寸靶材时,边缘效应造成的材料浪费更为显著。
1.3 背溅射与散射: “无的放矢”,徒劳的损耗
磁控溅射,并非一个完美无缺的“定向打击”过程。 溅射出的原子,并非全部都能按照预期的方向,精准地沉积到基片上。 一部分原子,会“调皮”地反弹回来,这就是背溅射;还有一部分原子,会在飞行途中与溅射气体分子碰撞,改变方向,发生散射。
(示意图:展示溅射原子飞离靶材表面后,一部分发生背溅射,一部分发生散射)
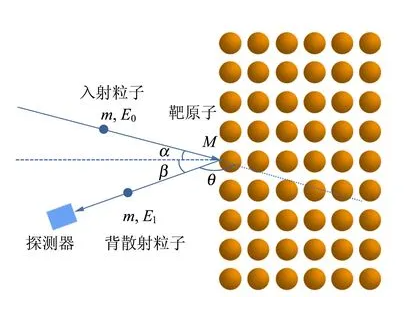
背溅射 主要是指溅射原子在离开靶材表面后,受到等离子体中离子或中性粒子的碰撞,反向散射回靶材表面。 这些背溅射原子,不仅无法沉积成膜,反而会重新轰击靶材表面,造成二次溅射,进一步加剧靶材的损耗,并可能影响薄膜的质量。
散射 则是指溅射原子在飞向基片的过程中,与溅射气体分子发生碰撞,改变了原有的运动方向。 散射后的原子,可能偏离基片区域,沉积到腔体壁上,或者以非最佳的角度沉积到基片上,影响薄膜的均匀性和致密度。 散射的程度与工作气压密切相关,气压越高,气体分子密度越大,散射现象越严重。
背溅射和散射,如同“无的放矢”,使得一部分宝贵的靶材材料白白损耗,无法转化为有用的薄膜,降低了材料的有效利用率。
1.4 靶材更换策略: “弃旧图新”,难以避免的浪费
靶材如同“消耗品”,在长时间的溅射过程中,会逐渐被腐蚀、消耗。 当靶材腐蚀到一定程度,无法满足薄膜质量要求或溅射速率过低时,就必须进行更换。 然而,即便更换下来的靶材,表面腐蚀不均匀,但往往仍有部分区域的材料尚未完全耗尽。 由于难以精确评估剩余材料的可用性,企业通常选择直接废弃旧靶材,更换全新的靶材。 这种“一刀切”式的更换策略,虽然简单粗暴,却造成了难以避免的材料浪费。
尤其对于贵金属靶材(如金、银、铂等)和高价值稀有金属靶材而言,这种浪费更令人痛心。 频繁更换靶材,不仅增加了材料成本,还带来了停机时间增加、生产效率降低等一系列负面影响。 如何优化靶材更换策略,最大限度地延长靶材使用寿命,减少材料浪费,是提升靶材利用率的重要环节。
2. 靶材利用率提升: 多维度技术突破与系统性解决方案
面对靶材利用率低下的多重挑战,科研人员和工程师们集思广益,从磁场调控、结构创新、工艺优化、材料回收等多个维度入手,研发出了一系列卓有成效的提升技术。这些技术如同“组合拳”,从不同层面击破靶材利用率的瓶颈,为降低生产成本、提高材料效率开辟了新的道路。
2.1 磁场优化技术: 精雕细琢,打造均匀等离子体“引擎”
磁场,是磁控溅射的灵魂。 优化磁场,如同为溅射系统打造一颗更强劲、更精准的“引擎”,驱动等离子体更均匀、更高效地工作。 磁场优化的核心目标,是实现靶材表面等离子体分布的均匀化,并增强等离子体约束,从而提高靶材的整体利用率。
2.1.1 平衡磁场与非平衡磁场: 应用场景的精细化匹配
磁场平衡度,是磁场优化设计中的一个重要参数。 根据磁场平衡度的不同,磁控溅射磁场可分为平衡磁场和非平衡磁场两大类,它们各有特点,适用于不同的应用场景。
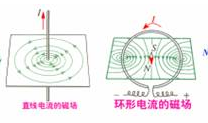
平衡磁场,其特点是磁力线主要闭合在靶材表面附近,对电子的约束能力较强,等离子体密度较高,溅射速率较快。 平衡磁场溅射的薄膜,离子轰击较弱,薄膜应力相对较小,适用于对薄膜应力要求较低的应用,例如装饰镀膜、光学镀膜等。
非平衡磁场 ,其特点是部分磁力线延伸到基片方向,可以引导一部分电子轰击基片表面,增强离子轰击,提高薄膜致密度和附着力。 非平衡磁场溅射的薄膜,离子轰击较强,薄膜应力相对较大,适用于对薄膜致密度和附着力要求较高的应用,例如工具涂层、硬质薄膜等。 但非平衡磁场也更容易导致靶材腐蚀不均匀。
在实际应用中,需要根据具体的镀膜应用需求,权衡薄膜性能和靶材利用率,选择合适的磁场平衡度。 例如,对于需要高致密度薄膜的应用,可以适当牺牲一些靶材利用率,选择非平衡磁场;而对于对成本控制要求较高的应用,则可以优先考虑平衡磁场,以提高靶材利用率。
2.1.2 旋转磁场技术: 动态磁场,均匀腐蚀的“魔术棒”
旋转磁场技术,如同为磁控溅射引入了一根“魔术棒”,通过动态地改变磁场分布,实现了靶材腐蚀的均匀化,大幅提升了靶材利用率。 旋转磁场靶,通常采用环形磁体,通过机械装置驱动磁体旋转,或者采用电磁铁阵列,通过控制电流实现磁场的旋转。 当磁体旋转时,靶材表面的磁场分布也随之动态变化,等离子体在靶材表面“扫描式”地移动,使得靶材各区域受到等同程度的溅射,最终实现均匀腐蚀。
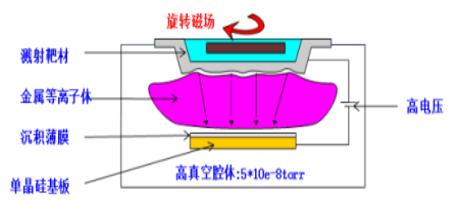
旋转磁场技术,尤其适用于大尺寸靶材和贵金属靶材。 对于大尺寸靶材,旋转磁场可以有效克服边缘效应,提高边缘区域的材料利用率;对于贵金属靶材,旋转磁场带来的利用率提升,可以直接转化为可观的经济效益。 然而,旋转磁场靶的结构相对复杂,制造成本和维护成本也较高。
2.1.3 多极磁场技术: 更精细的磁场“微调”,更优化的性能
多极磁场技术,如同为磁场优化提供了“微调”的手段,通过采用多极磁体结构,形成更复杂、更可控的磁场分布,实现了对等离子体约束和靶材腐蚀形貌的更精细调控。 多极磁场靶,通常采用多个磁极交替排列的磁体结构,例如,四极磁体、六极磁体、八极磁体等。 通过调节各个磁极的磁场强度和极性,可以灵活地控制靶材表面的磁场分布,实现对等离子体密度分布和溅射速率分布的精确调控,进一步优化靶材利用率和薄膜性能。
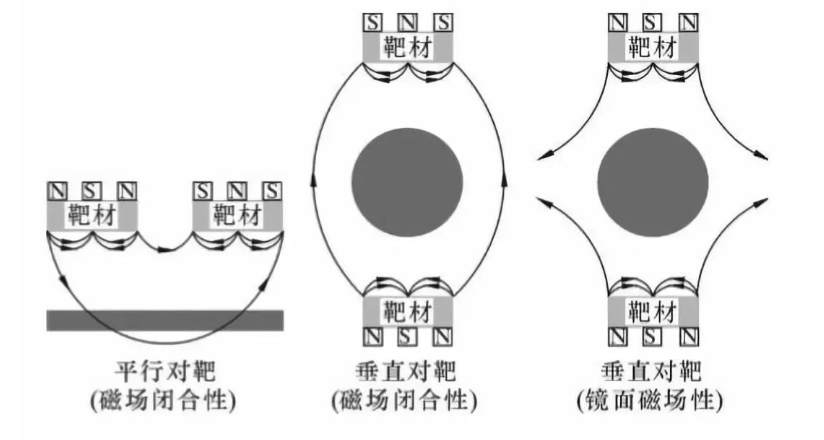
多极磁场技术,为高性能薄膜制备提供了更强大的磁场调控能力。 通过精细调节磁场分布,可以实现薄膜均匀性、致密度、应力、成分等多项性能指标的优化,满足更苛刻的应用需求。 然而,多极磁场靶的设计和制造难度也相对较高,需要更专业的磁场仿真和优化技术。
2.2 靶材结构创新设计: 突破“几何”瓶颈,提升材料固有利用率
磁场优化是从“外”部调控等离子体,而靶材结构创新则是从“内”部着手,通过改变靶材自身的几何形状,突破传统平面靶材的利用率瓶颈,直接提升材料的固有利用效率。
2.2.1 空心阴极靶: “中空”奥秘,倍增有效溅射面积
空心阴极靶,如同将传统的“实心”靶材,巧妙地改造成了“中空”结构,这一看似简单的结构变化,却蕴含着巨大的能量。 空心阴极靶,通常由两个相对放置的环形靶组成,中间形成一个空腔。 在溅射过程中,等离子体不仅在靶材外表面放电,还会在空腔内部放电,形成空心阴极放电效应。 空心阴极放电效应,能够显著提高空腔内部的等离子体密度,使得靶材的内表面也成为有效的溅射区域,从而倍增了靶材的有效溅射面积,大幅提升了靶材利用率。
空心阴极靶,尤其适用于制备高纯薄膜和贵金属薄膜。 其高溅射速率和高材料利用率,可以显著降低生产成本,并减少杂质污染,提高薄膜纯度。 然而,空心阴极靶的结构相对复杂,制造成本较高,且散热性能有待进一步优化。
2.2.2 分段式靶材: “化整为零”,延长靶材整体寿命
分段式靶材,如同将一块完整的靶材,“化整为零”,分割成多个独立的小块,这一巧妙的设计,旨在解决靶材腐蚀不均匀的问题,延长靶材的整体使用寿命,提高材料利用率。 分段式靶材,通常将靶材分割成同心圆环状、径向条状、棋盘格状等多种形式。 在溅射过程中,由于磁场和等离子体分布的不均匀性,靶材各区域的腐蚀程度不同。 当部分区域的靶材小块腐蚀殆尽时,只需更换这些小块,而其他区域的靶材仍可继续使用,无需整体更换靶材,从而延长了靶材的整体使用寿命,提高了材料利用率。
分段式靶材,尤其适用于大尺寸靶材和贵金属靶材。 对于大尺寸靶材,分段式设计可以有效降低靶材的制造成本和更换成本;对于贵金属靶材,分段式设计带来的寿命延长,可以显著降低材料消耗,节约成本。 然而,分段式靶材的结构相对复杂,制造和维护成本略有增加。
2.2.3 旋转靶: “滚筒式”溅射,均匀高效的典范
旋转靶,如同将靶材设计成一个“滚筒”,在溅射过程中不断旋转,实现了靶材表面的均匀腐蚀,成为了均匀高效溅射的典范。 旋转靶,通常采用圆柱形或筒形靶材,通过电机驱动靶材旋转。 在旋转过程中,靶材表面各区域轮流经过等离子体区域,受到均匀的溅射,避免了局部腐蚀过快的问题,大幅提升了靶材利用率,理论利用率可高达 80% 以上。 同时,旋转靶 sputtering 源 通常也配置强大的磁场系统,进一步约束等离子体,提高溅射效率和薄膜质量。
旋转靶,尤其适用于大面积均匀镀膜和高价值应用。 其镀膜均匀性好、靶材利用率高、可长时间稳定运行等优点,使其在高档显示面板、太阳能电池、半导体器件等领域得到了广泛应用。 然而,旋转靶溅射源 设备结构复杂,制造成本和维护难度都较高,投资较大。
2.2.4 阶梯靶与其他创新结构: 持续探索,永无止境
除了上述几种典型的创新靶材结构,研究人员还在不断探索各种新型靶材结构设计,例如,阶梯靶、弧形靶、锥形靶等,力求在靶材利用率、溅射速率、薄膜质量等方面取得更优异的性能。 阶梯靶,通过设计具有阶梯状表面的靶材,优化等离子体分布,改善靶材腐蚀均匀性,提高利用率。 其他创新结构设计,则更多地针对特定的应用需求和溅射工艺进行定制化开发,例如,用于提高反应溅射稳定性的活性靶材结构、用于实现多层膜成分精确控制的分区域靶材结构等。
2.3 工艺参数优化: 精益求精,挖掘现有设备的潜力
工艺参数,如同磁控溅射的“无形之手”,对溅射过程和薄膜性能产生着微妙而深刻的影响。 即使在既定的设备和靶材条件下,通过精细地优化工艺参数,也能在一定程度上提升靶材利用率,并改善薄膜质量。
2.3.1 工作气压优化: 散射与效率的“黄金平衡点”
工作气压,是磁控溅射工艺中一个至关重要的参数。 较低的工作气压,可以减少溅射原子与气体分子的碰撞散射,提高溅射原子的定向性,从而间接提升靶材利用率和薄膜致密度。 然而,过低的工作气压,会导致等离子体放电不稳定,溅射速率降低。 因此,需要寻找一个工作气压的“黄金平衡点”,在保证等离子体稳定放电和溅射速率的前提下,尽可能降低工作气压,减少散射损失,提升靶材利用率。
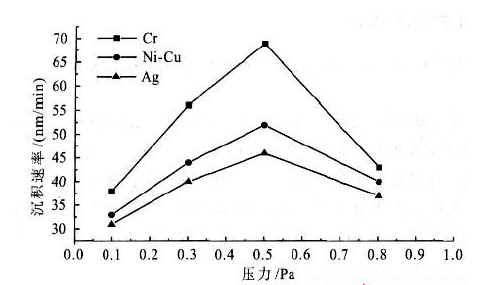
最佳工作气压的范围,与溅射气体种类、靶材材料、溅射功率、磁场强度等多种因素有关,需要通过实验优化确定。 对于反应溅射工艺,工作气压的优化更为复杂,需要同时考虑反应气体的分压和总压,以获得最佳的薄膜成分和溅射速率。
2.3.2 脉冲溅射技术: “脉冲”之力,突破反应溅射瓶颈
脉冲溅射技术,如同为直流溅射注入了一股“脉冲”能量,使其在反应溅射领域焕发出新的活力。 传统的直流溅射在进行反应溅射时,容易出现靶面中毒效应,导致溅射速率下降、放电不稳定等问题。 脉冲溅射技术,通过采用脉冲电源替代传统的直流电源,周期性地改变溅射电压的极性或幅度,可以有效地抑制靶面中毒效应,提高反应溅射的稳定性,并可能在一定程度上改善靶材利用率。
脉冲溅射技术,尤其适用于制备氧化物、氮化物等化合物薄膜。 其高稳定性、高沉积速率的特点,可以显著提高反应溅射的生产效率和薄膜质量。 脉冲溅射的脉冲频率、占空比等参数,也需要根据具体的应用需求进行优化,以获得最佳的溅射效果。
2.3.3 偏压溅射: “离子轰击”,提升沉积动力学
偏压溅射技术,如同为基片施加了一个“无形之手”,通过在基片上施加负偏压,吸引更多的Ar+离子轰击靶材,提高溅射速率,并改善薄膜的性能。 在偏压溅射过程中,负偏压会加速Ar+离子向靶材方向运动,增强离子轰击能量,提高靶材的溅射速率,从而在一定程度上提升靶材利用率。 同时,基片负偏压还可以增强离子轰击基片表面,提高薄膜的致密度、附着力、和表面形貌。
偏压溅射技术,常与其他靶材利用率提升技术协同使用,以获得更佳的综合效果。 例如,将偏压溅射与磁场优化、靶材结构创新等技术相结合,可以在提高靶材利用率的同时,显著改善薄膜的性能。 偏压电压的大小和施加方式,需要根据具体的应用需求进行优化,以避免引入过多的薄膜应力和缺陷。
2.4 材料回收与再利用: 变废为宝,构建绿色镀膜闭环
材料回收与再利用,如同为磁控溅射引入了“循环经济”的理念,将溅射过程中损失的靶材材料,通过先进的回收技术,变废为宝,重新投入生产,构建绿色镀膜的闭环系统。 尤其对于贵金属靶材和高价值稀有金属靶材而言,材料回收的经济效益和环保意义尤为显著。
2.4.1 背溅射回收技术: “亡羊补牢”,减少背向材料损失
背溅射回收技术,如同在靶材背面设置了一个“安全网”,将背溅射的靶材原子收集起来,防止其散失,实现“亡羊补牢”的效果。 背溅射回收装置,通常设置在靶材的背面,采用冷凝捕集、磁场约束等方式,收集背溅射的靶材原子,并定期进行回收和提纯。
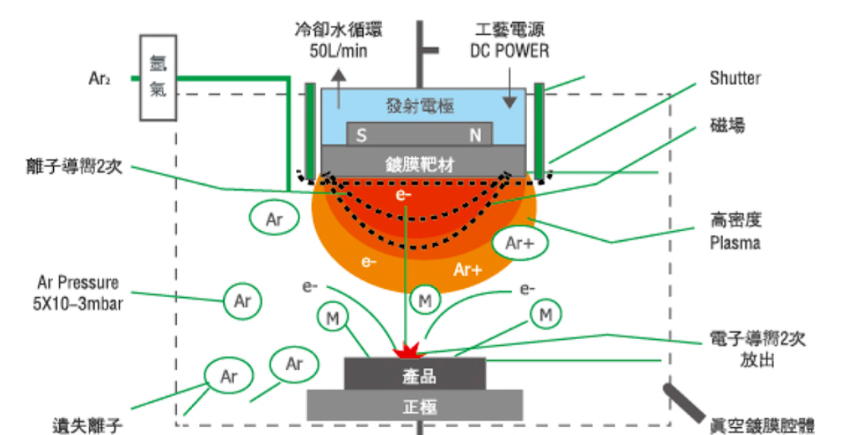
背溅射回收技术,尤其适用于高气压溅射和贵金属靶材溅射。 在高气压溅射中,背溅射现象较为严重,回收的效益更为显著;对于贵金属靶材,回收的经济价值更高。 背溅射回收装置的设计和维护,需要考虑回收效率、成本、以及对溅射工艺的影响等因素。
2.4.2 二次靶溅射技术: “废物利用”,腔体沉积物的华丽转身
二次靶溅射技术,如同为腔体壁上沉积的靶材材料,赋予了“第二次生命”,使其从“废物”变身为可再次利用的“资源”,实现了腔体沉积物的华丽转身。 在磁控溅射过程中,一部分溅射原子会散射到腔体壁上,形成沉积物。 二次靶溅射技术,利用额外的溅射源 (二次靶),将腔体壁上的沉积物再次溅射出来,重新沉积到基片上,提高整体的材料利用效率。
二次靶溅射技术,尤其适用于回收利用率较低的溅射工艺,例如,大面积镀膜、长寿命溅射等。 其优点是可以有效回收腔体壁上的沉积物,提高材料利用率,降低废弃物处理成本。 然而,二次靶溅射技术,设备结构较为复杂,工艺控制难度较高。
2.4.3 废旧靶材回收流程与规范: 构建靶材循环利用体系
废旧靶材回收,是构建靶材循环利用体系的关键环节。 对于更换下来的废旧靶材,进行专业的回收和提纯处理,提取有价值的金属材料,循环利用,可以大幅降低对原生矿产资源的依赖,实现靶材资源的可持续利用。 废旧靶材回收,通常包括预处理、破碎、溶解、萃取、电解、提纯等多个工艺步骤,需要专业的回收设备和技术。 行业内也逐步建立起废旧靶材回收的标准和规范,引导企业规范化、规模化地开展靶材回收业务,构建完整的靶材生命周期管理体系。
3. 成本效益分析与应用场景选择: 理性决策,价值最大化
各种靶材利用率提升技术,如同“百花齐放”,各有优势,也各有局限。 企业在选择技术方案时,需要进行全面的成本效益分析,并结合自身的应用场景,做出理性的决策,实现价值最大化。
技术手段 |
优点 |
缺点 |
成本投入 |
实施难度 |
利用率提升幅度 |
典型应用场景 |
---|---|---|---|---|---|---|
磁场优化 |
成本相对较低,通用性强,对多种溅射类型均有效,操作相对简便 |
提升幅度受限于磁场优化空间,需要专业磁场设计知识和经验 |
低 |
中 |
中-高 |
各种磁控溅射应用,尤其适用于对成本敏感,追求一定效率提升的场景 |
空心阴极靶材 |
利用率提升显著,等离子体密度高,可实现高溅射速率,适用于高纯薄膜制备 |
靶材结构复杂,制造成本较高,散热设计需优化,对电源匹配性要求较高 |
高 |
中 |
高 |
贵金属靶材溅射,高价值稀有金属靶材溅射,高纯薄膜制备,对利用率和溅射速率要求极高的场合 |
分段式靶材 |
延长靶材整体寿命,减少更换频率,降低维护成本,适用于大尺寸靶材和腐蚀不均匀靶材 |
结构相对复杂,制造精度要求较高,分段接缝处可能影响薄膜均匀性,更换分段靶材块操作略复杂 |
中 |
中 |
中 |
大尺寸靶材溅射,贵金属靶材溅射,合金靶材溅射,腐蚀不均匀靶材溅射,追求长寿命和降低更换频率的场景 |
旋转靶材 |
利用率极高,镀膜均匀性优异,可实现大面积均匀镀膜,适用于高品质薄膜制备 |
设备结构极其复杂,制造成本极其高昂,维护难度大,投资回报周期较长,对工艺控制精度要求极高 |
高 |
高 |
高 |
大面积均匀镀膜,高品质光学薄膜制备,高档显示面板镀膜,太阳能电池镀膜等高价值应用 |
工艺参数优化 |
成本极低,易于实施,操作灵活,无需硬件改造,即可在现有设备基础上进行优化 |
提升幅度相对有限,需在薄膜质量和靶材利用率之间权衡,优化空间受限于设备自身性能 |
低 |
低 |
低-中 |
各种磁控溅射应用,尤其适用于对成本控制严格,追求低成本、快速优化的场景 |
材料回收与再利用 |
资源节约,环保效益显著,经济效益高 (尤其对于贵金属靶材),可构建绿色循环镀膜体系 |
回收工艺相对复杂,初期设备投入和技术研发成本较高,回收效率和纯度受多种因素影响,回收体系的建立和运营需长期投入 |
中-高 |
中-高 |
中-高 |
贵金属靶材溅射,高价值靶材溅射,大批量生产,环保法规要求严格的行业,追求可持续发展和循环经济的场景 |
4. 未来发展趋势: 智能化、精细化、可持续的靶材高效利用之路
展望未来,随着薄膜技术应用的不断拓展,以及全球对绿色制造和可持续发展的日益重视,磁控溅射靶材利用率提升技术必将迎来更加广阔的发展空间。 未来的发展趋势,将主要体现在智能化、精细化和可持续化三个方面:
4.1 智能化控制技术: 迈向自优化的靶材利用率管理
智能化控制技术,将为磁控溅射靶材利用率提升注入“智慧”的基因,实现从人工经验优化到智能自主优化的跨越。 未来,结合 传感器技术、大数据分析、人工智能算法 的智能化控制系统,将能够对磁控溅射工艺进行实时监控、智能诊断和自主优化:
(示意图:展示智能化控制系统通过传感器采集数据,AI算法分析优化工艺参数)
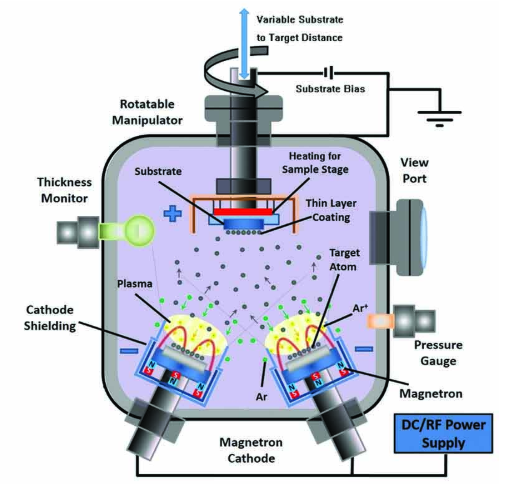
智能化控制技术,将实现靶材利用率管理的自动化、精细化和高效化,大幅降低人工干预,提高生产效率,并为实现更高水平的靶材利用率提供有力支撑。
-
实时监控: 利用传感器实时监测等离子体参数 (密度、温度、辉光强度等)、靶材腐蚀状态 (电压、电流、溅射速率等)、薄膜质量 (厚度、均匀性、应力等) 等关键数据。
-
智能诊断: 基于大数据分析和人工智能算法,对实时监测数据进行分析,诊断靶材利用率低下的原因,例如,非均匀腐蚀程度、边缘效应损失比例、背溅射强度等。
-
自主优化: 根据智能诊断结果,自主优化工艺参数 (溅射功率、工作气压、气体流量等)、磁场分布 (动态调节磁体电流、旋转速度等)、靶材更换策略等,最大限度地提升靶材利用率,并保持薄膜质量的稳定性和一致性。
4.2 新型靶材结构与材料: 持续创新的“源头活水”
新型靶材结构与材料的创新,将为靶材利用率提升提供源源不断的“活水”。 未来的靶材结构设计,将更加注重 功能化、定制化和集成化:
在靶材材料方面,高纯靶材、纳米晶靶材、合金靶材 等新型材料将成为发展趋势:
-
功能化靶材: 开发具有特殊功能的靶材结构,例如,自适应磁场靶材 (根据溅射状态动态调整磁场分布)、可控腐蚀形貌靶材 (预设腐蚀形貌,提高特定区域利用率) 等。
-
定制化靶材: 根据特定的应用需求,定制化设计靶材结构和尺寸,最大限度地匹配工艺要求,提高材料利用率。
-
集成化靶材: 将多种靶材利用率提升技术集成于一体,例如,将空心阴极结构、分段式结构、旋转磁场技术等集成到同一靶材上,实现多技术协同增效。
-
高纯靶材: 更高纯度的靶材,可以提高薄膜的纯度和性能,并减少杂质引起的溅射异常,提高靶材利用率。
-
纳米晶靶材: 采用纳米晶结构的靶材,可以提高靶材的溅射速率和均匀性,改善薄膜质量,并可能在一定程度上提升靶材利用率。
-
合金靶材优化设计: 针对特定合金靶材,优化合金成分配比和制备工艺,提高靶材的溅射性能和耐腐蚀性,延长靶材使用寿命,提升利用率。
4.3 高效回收与循环利用: 构建绿色、可持续的镀膜产业生态
高效回收与循环利用技术,将成为构建绿色、可持续镀膜产业生态的关键支柱。 未来的靶材回收技术,将朝着 高效化、低成本化、环保化 的方向发展:
未来,将建立更加完善的靶材生命周期管理体系,从靶材设计、制造、使用、回收、再利用等各个环节,实现资源的高效循环利用,最大限度地减少资源浪费和环境污染,构建真正绿色、可持续的镀膜产业生态。
-
高效回收技术: 开发更高效的背溅射回收装置、二次靶溅射系统,以及废旧靶材回收工艺,大幅提高回收效率和材料纯度。
-
低成本回收技术: 降低回收设备的投资成本和运行成本,简化回收工艺流程,提高回收的经济性,使更多企业愿意投入到靶材回收业务中。
-
环保化回收技术: 采用更环保的回收工艺,减少二次污染,实现靶材回收过程的绿色化。