不同类型的磁控溅射技术比较:直流、射频、脉冲磁控溅射的优缺点分析
1. 磁控溅射技术原理概述
磁控溅射技术的核心在于利用磁场约束电子,增强等离子体密度,从而高效溅射靶材原子并沉积成膜。 在传统二极溅射基础上,磁控溅射引入与电场正交的磁场,典型的磁场构型会在靶面形成闭合磁力线,构成“磁阱”。 电子在电场和磁场的共同作用下,运动轨迹呈螺旋状,被有效地束缚在靶材表面附近的等离子体区域,增加了电子与工作气体原子碰撞电离的几率,显著提升了等离子体密度和电离效率。
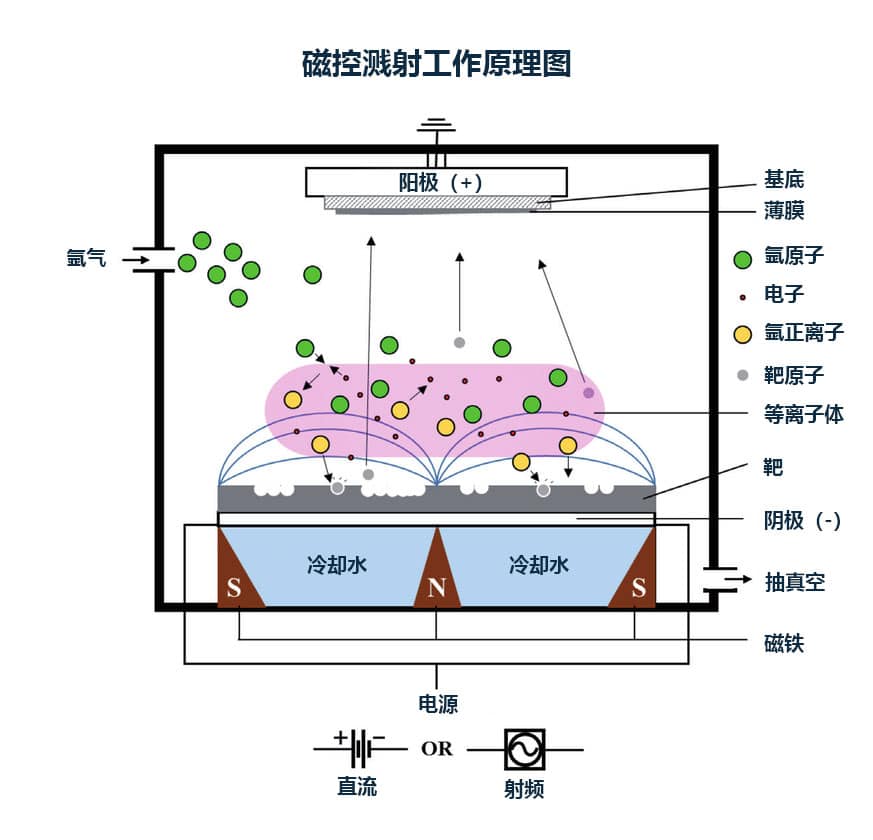
磁控溅射的共通优势体现于:
- 高效率溅射: 磁场约束极大提升等离子体利用率,实现高沉积速率。单位功率下,磁控溅射速率远高于传统溅射。
- 低气压操作: 高密度等离子体允许在较低工作气压下溅射,减少气体散射,提升薄膜均匀性和纯度。
- 靶材高效利用: 磁场集中等离子体在靶面,能量集中,降低非溅射区域的损耗,延长靶材使用寿命。
- 薄膜高附着力: 溅射原子能量可控,适度的离子轰击有助于提升薄膜与基底的结合强度。
- 材料普适性强: 通过技术变型,可溅射金属、合金、化合物、乃至聚合物等多元材料。
2. 不同类型磁控溅射技术详解
深入剖析直流、射频和脉冲磁控溅射的技术细节,对比其原理差异、工艺特点、薄膜特性及应用范畴。
2.1 直流 (DC) 磁控溅射
2.1.1 工作原理及技术特点
直流磁控溅射是最为基础和广泛应用的磁控溅射形式。 其核心构成简洁:直流电源在阴极靶和阳极基片间施加恒定负电压,引发辉光放电。 工作气体(通常为氩气)被电离,产生的氩离子 (Ar+) 在电场加速下高速轰击阴极靶材。 动量传递效应使得靶材表面的原子或原子团被溅射出来。溅射出的原子呈中性,飞向基片并在其表面凝结成膜。二次电子在电磁场约束下,维持等离子体放电,形成自持放电过程。
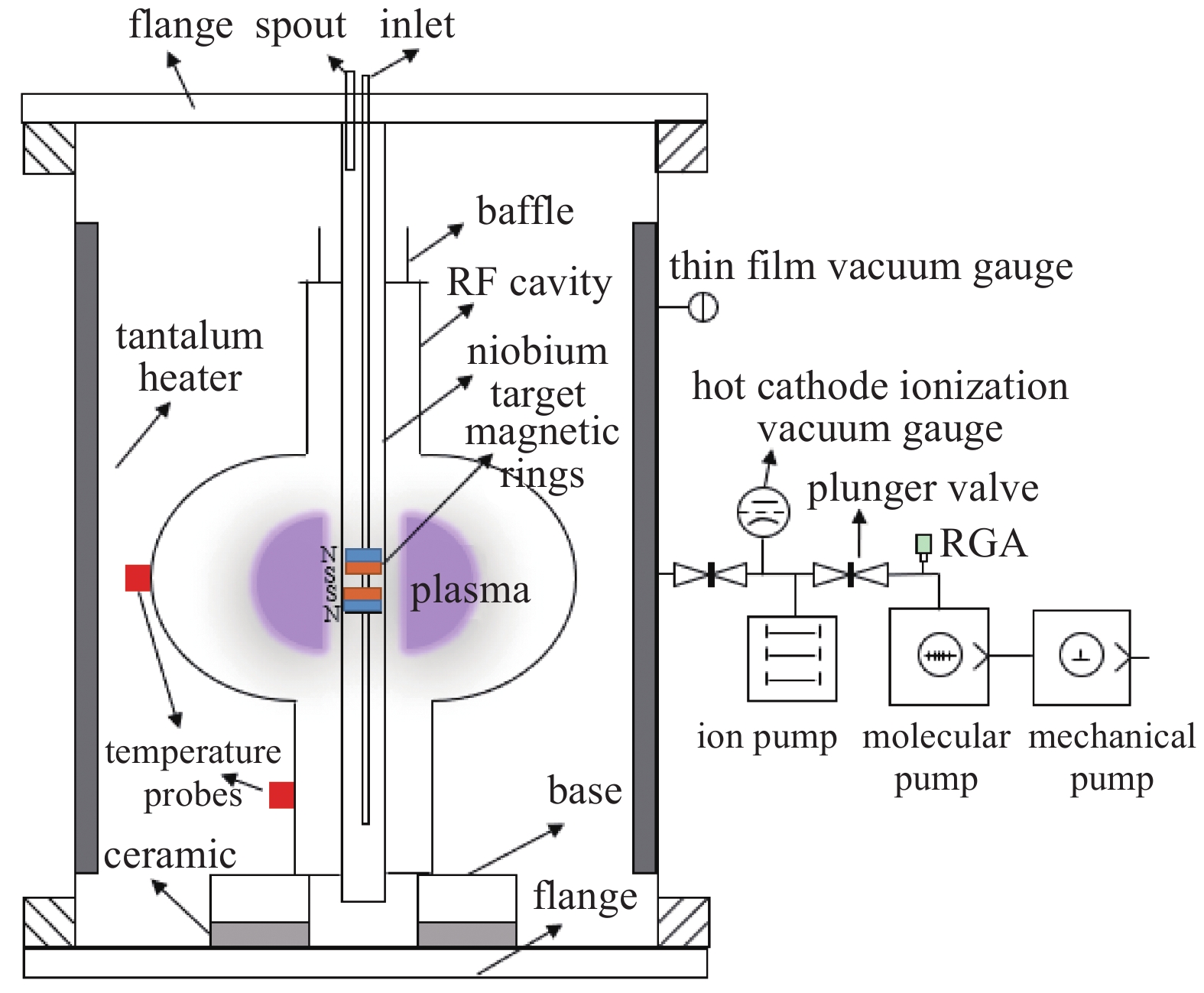
直流磁控溅射的技术优势在于:
- 结构极简与低成本: 直流电源系统成熟、稳定、廉价,设备维护简易,运行成本低。
- 溅射速率突出: 对于金属等良导体靶材,直流放电高效稳定,可实现较高的溅射速率,满足工业规模化生产需求。
- 工艺成熟度高: DC 溅射技术发展历史悠久,工艺参数易于控制,工艺窗口宽泛,量产经验丰富。
2.1.2 局限性分析
- 靶材导电性制约: 直流溅射的致命弱点在于无法有效溅射绝缘靶材。 绝缘靶材表面在正离子轰击下易积累正电荷,形成正电荷层。 这层正电荷会反向排斥入射的正离子,并吸引电子,最终抑制等离子体的维持和离子轰击,导致溅射过程停滞,即所谓的“靶充电效应”或“靶中毒”。 此外,对于半导体靶材,若电阻率过高,也会出现类似问题,限制了DC溅射的应用范围。
- 易发打火 (Arcing) 现象: 在直流高压放电过程中,特别是在靶面污染、表面状态不佳或工作气压不稳定时,容易发生局部放电击穿,产生瞬时大电流的打火现象。 打火不仅会损伤靶材,降低靶材寿命,还会产生宏观颗粒溅射到薄膜中,严重劣化薄膜质量,并影响工艺稳定性。特别是在反应溅射制备化合物薄膜时,靶面易生成绝缘层,更易诱发打火。
2.1.3 典型应用
直流磁控溅射凭借其高性价比,在诸多领域占据重要地位:
- 装饰镀膜: 制备金、银、铬等金属装饰膜层,如手表壳体、眼镜框架、汽车饰件等。
- 工具硬质涂层: 沉积 TiN, CrN 等硬质金属氮化物薄膜,提升刀具、模具的耐磨性和使用寿命。
- 微电子互连线: 铝、铜等金属薄膜作为集成电路中的互连线,实现电路信号的传输。
- 太阳能电池背电极: 铝、银等金属背电极,提升太阳能电池的光电转换效率。
2.2 射频 (RF) 磁控溅射
2.2.1 工作原理及技术特点
为突破直流溅射在绝缘靶材应用上的瓶颈,射频磁控溅射应运而生。 RF溅射采用高频射频电源(常用频率为 13.56 MHz)取代直流电源。 在高频交变电场作用下,等离子体中电子和离子均可被加速。由于电子质量远小于离子,电子的响应速度远快于离子,在高频电场中,电子更易被加速并撞击靶材。 当射频电压施加在靶材上时,靶材表面在射频周期内会交替受到正负离子的轰击,从而实现对绝缘靶材的有效溅射。

自偏压效应 (Self-Bias): RF 溅射的关键在于自偏压效应。 由于电子迁移率远高于离子,在射频周期内,靶材表面积累的电子数量远多于正离子,导致靶材的平均电位为负值,形成负自偏压。 负自偏压的建立,使得正离子能在有效电场力驱动下轰击靶材,实现溅射。 自偏压的大小与等离子体参数、射频功率、二次电子发射系数等因素密切相关。
射频磁控溅射的技术优势:
- 全材料溅射能力: RF 溅射可溅射包括金属、合金、氧化物、氮化物、陶瓷、玻璃、聚合物等在内的几乎所有固态材料,极大地拓展了磁控溅射技术的应用范围。
- 显著降低打火: 高频射频电源能够在每个射频周期内快速中和积聚在绝缘靶材表面的电荷,有效抑制靶充电效应和打火现象,提高工艺稳定性,尤其是在反应溅射制备绝缘化合物薄膜时优势明显。
2.2.2 局限性分析
- 沉积速率相对较低: 相比 DC 溅射,RF 溅射的沉积速率通常偏低。 原因在于射频功率的能量转换效率相对较低,且射频匹配网络在功率传输过程中存在能量损耗。此外,为了保证绝缘靶材的溅射效率和薄膜质量,通常需要降低射频功率,进一步降低了沉积速率。
- 设备复杂性与高成本: RF 溅射系统需要复杂的射频电源、射频匹配网络、高频传输电缆等组件,设备结构更复杂,制造成本和维护成本均显著高于 DC 溅射系统。
- 工艺控制难度增加: RF 溅射工艺参数更多,如射频功率、工作气压、自偏压、匹配网络调节等,参数优化和工艺控制相对复杂,对操作人员的技术水平要求更高。
2.2.3 典型应用
射频磁控溅射凭借其 универсальность 材料溅射能力,在诸多高技术领域不可或缺:
- 半导体器件制造: 沉积 SiO2, Si3N4 等绝缘薄膜,作为 MOSFET 的栅极绝缘层、器件钝化保护层、多层互连的介质层等关键结构。
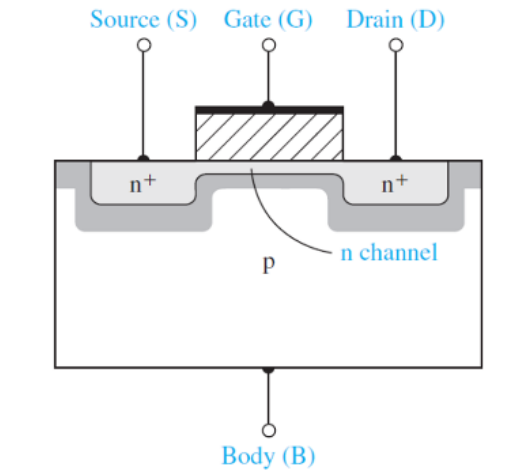
光学薄膜制备: 制备各类光学功能薄膜,如减反射膜、高反射膜、滤光片、偏振片等,广泛应用于光学仪器、显示器件、光通信器件等领域。
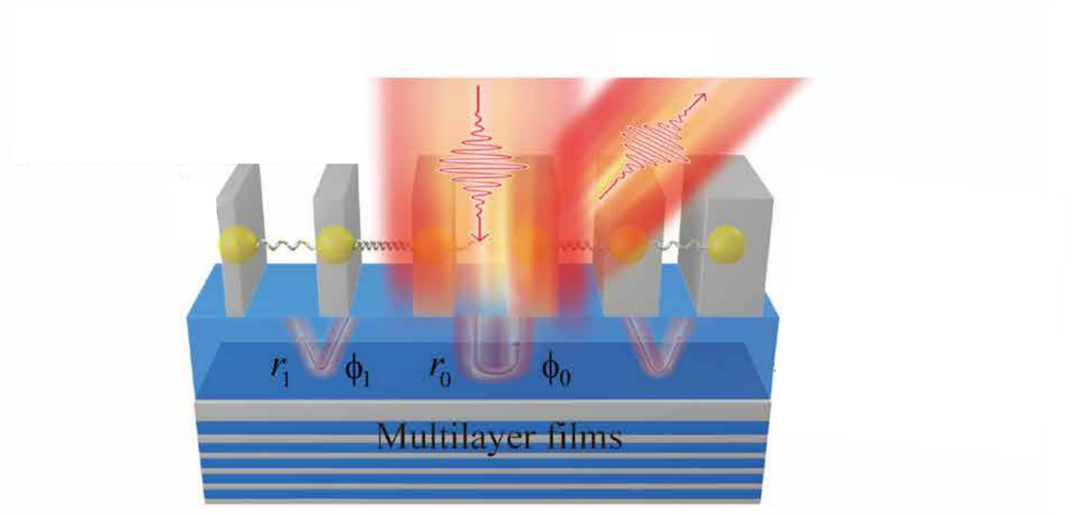
- 透明导电薄膜 (TCO): 制备 ITO (氧化铟锡), AZO (掺铝氧化锌) 等 TCO 薄膜,应用于触摸屏、液晶显示器、太阳能电池等,是现代光电子产业的重要基石。
- 聚合物薄膜制备: 利用 RF 等离子体聚合技术,制备功能化聚合物薄膜,应用于生物医用材料、柔性电子、传感器件等新兴领域。
2.3 脉冲 (Pulsed) 磁控溅射
2.3.1 工作原理及技术特点
脉冲磁控溅射是在 DC 磁控溅射基础上发展出的改良技术。 它采用脉冲直流电源替代传统恒定直流电源,在靶材上施加周期性脉冲电压。 脉冲电压波形由脉冲开启时间 (Ton) 和脉冲关闭时间 (Toff) 构成,通过调控脉冲频率、占空比(Ton/(Ton+Toff))等参数,可精细调控溅射过程。
脉冲模式分类:
- 单极脉冲溅射 (Unipolar Pulsed Sputtering): 脉冲电压在正电压与零电压间切换,脉冲关闭期间,靶材电压回零。
- 双极脉冲溅射 (Bipolar Pulsed Sputtering): 脉冲电压在正电压与负电压间切换,负向脉冲电压可用于反向溅射,更有效地清除靶面污染物,并抑制靶中毒。 双极脉冲溅射在反应溅射中应用更为普遍。
脉冲磁控溅射的技术优势:
- 高效抑制打火 (Arcing): 脉冲关闭期 (Toff) 为靶材表面积累的正电荷提供了释放和中和的时间窗口,有效抑制了打火现象的发生,大幅提升了工艺稳定性,尤其在反应溅射制备化合物薄膜时效果显著。 脉冲频率和占空比是抑制打火的关键参数。
- 改善薄膜微结构与性能: 脉冲溅射通过调控脉冲参数,可以调节溅射粒子的能量分布和入射通量,进而控制薄膜的成核与生长过程,优化薄膜的致密度、均匀性、应力、晶粒尺寸、取向等微观结构,最终改善薄膜的宏观性能。 例如,脉冲溅射可制备出更为致密的氧化物薄膜,提升其介电性能和阻隔性能;可调控薄膜应力,提升薄膜与基底的结合强度,降低膜层开裂风险。
- 提升反应溅射速率: 脉冲溅射允许采用更高的平均功率进行溅射,同时抑制打火,在反应溅射中可获得更高的沉积速率,突破传统 DC 反应溅射的速率瓶颈。
- 拓展材料溅射范围: 相比 DC 溅射,脉冲溅射可用于溅射部分半绝缘材料和高阻抗靶材,材料适用范围有所拓展。
2.3.2 局限性分析
- 设备与工艺复杂性提升: 脉冲溅射系统需配备专用脉冲电源和更精密的控制系统,设备成本和工艺调控难度均有所增加。 脉冲参数(频率、占空比、脉冲波形等)与薄膜性能之间存在复杂的非线性关系,工艺优化更具挑战性。
- 平均沉积速率可能降低: 为抑制打火和提升膜质量,脉冲溅射有时需降低平均功率(通过降低占空比或峰值功率实现),导致平均沉积速率可能较 DC 溅射有所降低。 但这通常可以通过优化脉冲参数来弥补,例如采用高功率短脉冲模式。
2.3.3 典型应用
脉冲磁控溅射凭借其独特的优势,在高性能薄膜制备领域展现出广阔的应用前景:
- 反应溅射制备高性能化合物薄膜: 在制备氧化物 (如 ITO, Al2O3, TiO2)、氮化物 (如 TiN, Si3N4)、碳化物 (如 DLC) 等化合物薄膜时,脉冲溅射能有效克服靶中毒和打火问题,获得高质量薄膜。 例如,制备高透明、低电阻的 ITO 薄膜,高致密、低缺陷的介质薄膜,以及高硬度、低摩擦系数的硬质保护薄膜等。
- 制备纳米结构与多层膜: 通过脉冲溅射,可精确控制薄膜的纳米尺度结构,制备纳米多层膜、梯度成分膜、纳米晶薄膜等,实现薄膜功能化的设计与调控。 例如,制备周期性多层膜反射镜、量子阱结构薄膜、纳米复合硬质涂层等。
- 大面积均匀镀膜: 脉冲溅射在制备大面积均匀薄膜方面具有优势,适合应用于平板显示、柔性电子、太阳能电池等大面积器件的薄膜制备。
3. 三种磁控溅射技术的对比分析
为更清晰地对比直流、射频和脉冲磁控溅射技术的差异,表1 从靶材适用性、沉积速率、薄膜质量、打火抑制、设备复杂度、成本以及典型应用等关键指标进行了对比总结。
表1:直流、射频和脉冲磁控溅射技术对比
技术类型 | 直流磁控溅射 (DC) | 射频磁控溅射 (RF) | 脉冲磁控溅射 (Pulsed) |
---|---|---|---|
靶材适用性 | 导电材料 | 导电/绝缘材料 | 导电/半绝缘/部分绝缘材料 |
沉积速率 | 高 | 中等 | 中等至高 (可优化) |
薄膜质量 | 一般 | 一般至良好 | 良好至优秀 (可调控) |
打火抑制 | 易产生 | 较少 | 有效抑制 |
设备复杂度 | 简单 | 复杂 | 较复杂 |
设备成本 | 低 | 高 | 较高 |
工艺控制难度 | 简单 | 较复杂 | 较复杂 |
核心优势 | 结构简易、速率高、成本低 | 材料普适、打火少 | 抑制打火、质量可控、反应溅射优势 |
主要局限 | 靶材受限、易打火 | 速率较低、成本高 | 设备工艺复杂 |
典型应用 | 金属膜、装饰镀膜 | 绝缘膜、光学膜 | 化合物膜、高性能膜、大面积镀膜 |
4. 应用实例剖析
直流磁控溅射应用: 铝背电极制备
在晶硅太阳能电池制造中,背电极通常采用直流磁控溅射沉积铝膜。 铝金属具有优异的导电性、良好的光反射率以及低廉的成本,完美契合太阳能电池背电极的应用需求。 DC 溅射铝膜工艺成熟、速率高、成本可控,能满足太阳能电池大规模生产的要求。
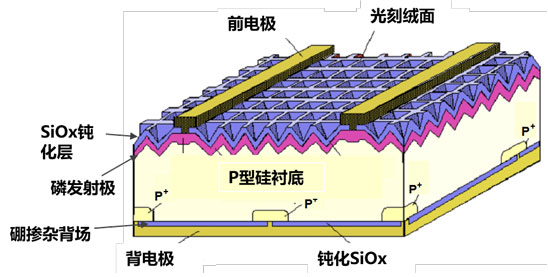
射频磁控溅射应用: SiO2 栅极绝缘层
在薄膜晶体管 (TFT) 液晶显示面板中,栅极绝缘层是核心功能层之一。 射频磁控溅射常用于沉积二氧化硅 (SiO2) 或氮化硅 (SiNx) 薄膜作为栅极绝缘层。 SiO2 和 SiNx 具有优异的绝缘性能、良好的界面特性以及化学稳定性,能有效阻止栅极与沟道间的漏电流,保障 TFT 器件的可靠运行。 RF 溅射技术能够高质量沉积绝缘性良好的 SiO2 和 SiNx 薄膜,满足平板显示产业对高性能绝缘层的需求。
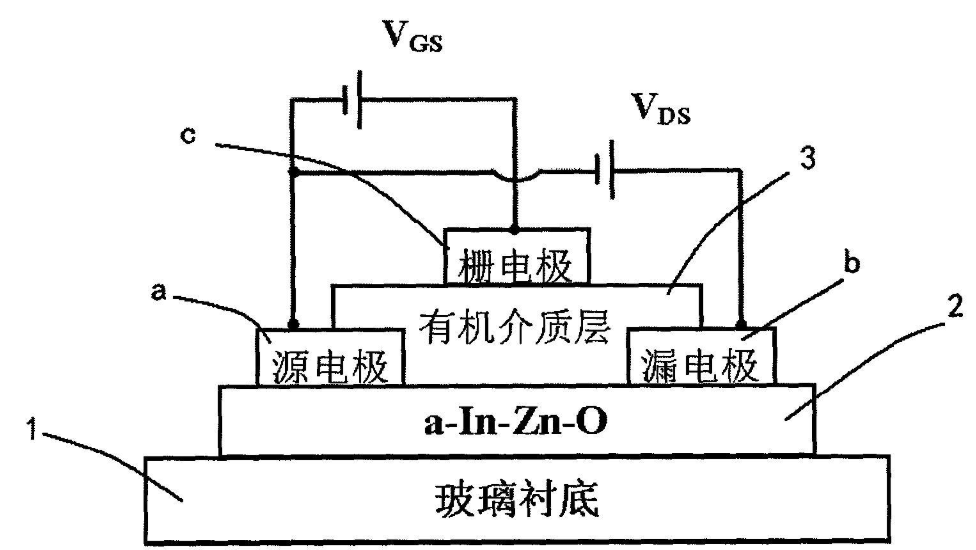
脉冲磁控溅射应用: 高反射率多层膜系
高精度光学仪器和激光系统中,常需要使用高反射率的多层膜系,例如介质反射镜 (DBR)。 脉冲磁控溅射技术在制备此类高性能光学薄膜中优势突出。 通过精确控制脉冲参数,脉冲溅射能够制备出致密度更高、界面更清晰、应力更可控的薄膜层, 从而显著提升多层膜的光学性能,如反射率、带宽、光谱特性等,并提高膜层的长期稳定性。
直流、射频与脉冲磁控溅射技术各有千秋,分别适用于不同的应用场景。 DC 溅射凭借其经济性和高效率,在导电薄膜领域仍占据主导地位。 RF 溅射以其材料的广泛适应性,成为绝缘薄膜制备的关键技术。 脉冲溅射则以其在薄膜质量调控和反应溅射方面的优势,在高性能薄膜领域展现出巨大的潜力。
未来,磁控溅射技术的发展趋势将聚焦于以下几个方向:
- 更高性能薄膜制备: 发展更精密的磁控溅射技术,如高功率脉冲磁控溅射 (HiPIMS)、中频磁控溅射、同步溅射等,以制备更致密、更均匀、成分更可控、性能更优异的薄膜,满足日益增长的高端应用需求。
- 低成本绿色制造: 研发更高效、节能、环保的磁控溅射设备和工艺,降低制造成本,减少环境污染,推动薄膜技术的可持续发展。
- 拓展新兴应用领域: 探索磁控溅射技术在生物医疗、柔性电子、能源存储、先进传感等新兴领域的应用,开辟新的增长空间。